The calcium hydroxide production line adopts a double-shaft stirring structure and consists of a bucket elevator, a special pulse dust collector, a digester, a semi-finished product conveyor, a powder separator, and a PLC control system. The calcium production line has a series of advantages such as environmental protection, automation, and reduction of labor consumption. So do you know the use of calcium hydroxide production line, what should we pay attention to, and how should we ensure the quality of calcium hydroxide in the production process ?
Precautions for the use of calcium hydroxide production line?
1. Calcium hydroxide production line usually works in a high temperature environment, the ambient temperature is high, and the normal working equipment will emit a lot of heat. Therefore, some equipment on the calcium hydroxide production line may generate heat due to continuous work during the production process. We need to prepare some cooling and freezing devices to cool down the equipment when needed to avoid wear and tear of components.
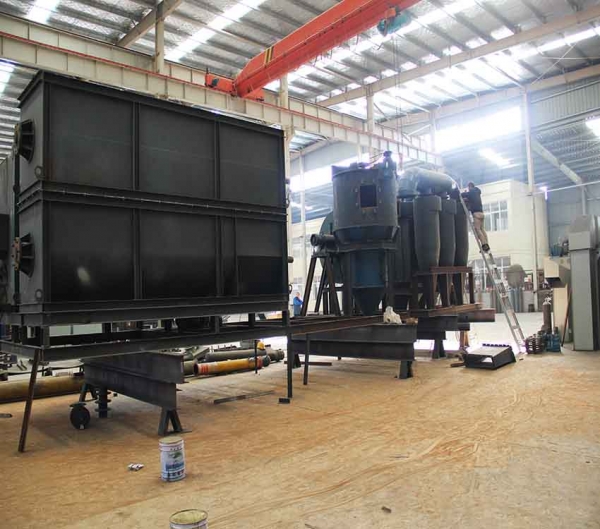
2. When working in a high temperature environment, we need to consider the safety and reliability of electricity consumption to ensure that the calcium hydroxide equipment and the circuit of the production line workshop are smooth. The calcium hydroxide equipment can be matched with some electrical equipment , and the detection of electrical equipment can be done in time. If it is found that the line is aging or abnormal, it should be stopped in time.
3. Do a good job in the anti-rust and anti-corrosion measures of the calcium hydroxide production line. Such as long-term rust prevention on exposed metal surfaces, that is, unpainted places: coating and electroplating processes can be used, and corrosion-resistant alloys can be used to prevent rust in the later stage. This work can be started from two aspects, one is to paint the equipment, and the other is to do a good job in post-maintenance and cleaning of the equipment to reduce the probability of rusting of calcium hydroxide equipment.
…
Details can be accessed here: https://www.ly-gaifeng.com/blog/the-use-of-calcium-hydroxide-production-line.html